OCEAN-GOING OVERHEAD TRAVELLING CRANE
Condra is to manufacture its first seagoing crane, an overhead maintenance machine with power-to-motion conversion achieved through rack-and-pinion instead of pure friction.
The order has been received and work has begun. Delivery will take place soon after completion mid-year, well ahead of shipboard installation and commissioning scheduled for November-December.
The crane will be used for maintenance work on helicopters and other equipment within a deck-level workshop, where the 2 ton, 4 metre-span, double-girder electric overhead travelling machine will carry out its duties at sea as well as in port. Notably, maintenance work will often be executed while the vessel is negotiating the Atlantic Ocean, notorious for its storms.
It was because of the customer’s need to be able to use the crane in moderately rough seas that Condra’s engineers proposed drive through rack-and-pinion.
The machine has to be able to work while the ship is rolling or pitching through arcs of up to 30 degrees, or 15 degrees either side of the vertical, an oscillation that would pose a challenge to conventionally designed long-travel and cross-travel movement, in which motor power is applied to steel wheels and the friction between wheel and girder produces motion. Oscillation of the ship would cause the wheels of such a design to slip, and the crane would run away.
To meet the design specification, Condra therefore replaced all wheels on the long-travel and cross-travel with rack-and-pinion arrangements that will deliver both traction and stability as the ship moves about.
440-volt three-phase motors will be used to drive the pinions along their racks, maintaining a constant speed and countering the varying gravitational component while the vessel rolls and pitches. When stormy seas force a deviation greater than a 30-degree arc, work in the workshop will stop and the crane will be secured via its bottom-block (hook) to a structural girder on the workshop’s walls to make accidental movement impossible.
Condra has made use of rack-and-pinion drives before, in cranes designed to operate in high winds.
Commenting on the order, Condra managing director Marc Kleiner said that the design of the crane had proved interesting not only because of the need to use rack-and-pinion drives, but also because of the very tight installation parameters within the vessel’s workshop, where ventilation pipes impose limits on the available space, and where careful design of the crane’s structure was needed to allow the hoist to be situated almost touching the workshop roof, thereby providing maximum lifting height.
“The resulting design is an underslung crane attached to the gantry beam rather than to the gantry columns. With the hoist sitting astride the underslung girders, we are able to give the customer the lifting height that he wants,” Kleiner said.
“It will be a compact but very effective arrangement.”
After delivery of the seagoing crane a few months from now, Condra technicians will carry out installation and commissioning in Durban at a much later date convenient to the customer, probably towards the end of the year when the vessel returns to harbour.
The order has been received and work has begun. Delivery will take place soon after completion mid-year, well ahead of shipboard installation and commissioning scheduled for November-December.
The crane will be used for maintenance work on helicopters and other equipment within a deck-level workshop, where the 2 ton, 4 metre-span, double-girder electric overhead travelling machine will carry out its duties at sea as well as in port. Notably, maintenance work will often be executed while the vessel is negotiating the Atlantic Ocean, notorious for its storms.
It was because of the customer’s need to be able to use the crane in moderately rough seas that Condra’s engineers proposed drive through rack-and-pinion.
The machine has to be able to work while the ship is rolling or pitching through arcs of up to 30 degrees, or 15 degrees either side of the vertical, an oscillation that would pose a challenge to conventionally designed long-travel and cross-travel movement, in which motor power is applied to steel wheels and the friction between wheel and girder produces motion. Oscillation of the ship would cause the wheels of such a design to slip, and the crane would run away.
To meet the design specification, Condra therefore replaced all wheels on the long-travel and cross-travel with rack-and-pinion arrangements that will deliver both traction and stability as the ship moves about.
440-volt three-phase motors will be used to drive the pinions along their racks, maintaining a constant speed and countering the varying gravitational component while the vessel rolls and pitches. When stormy seas force a deviation greater than a 30-degree arc, work in the workshop will stop and the crane will be secured via its bottom-block (hook) to a structural girder on the workshop’s walls to make accidental movement impossible.
Condra has made use of rack-and-pinion drives before, in cranes designed to operate in high winds.
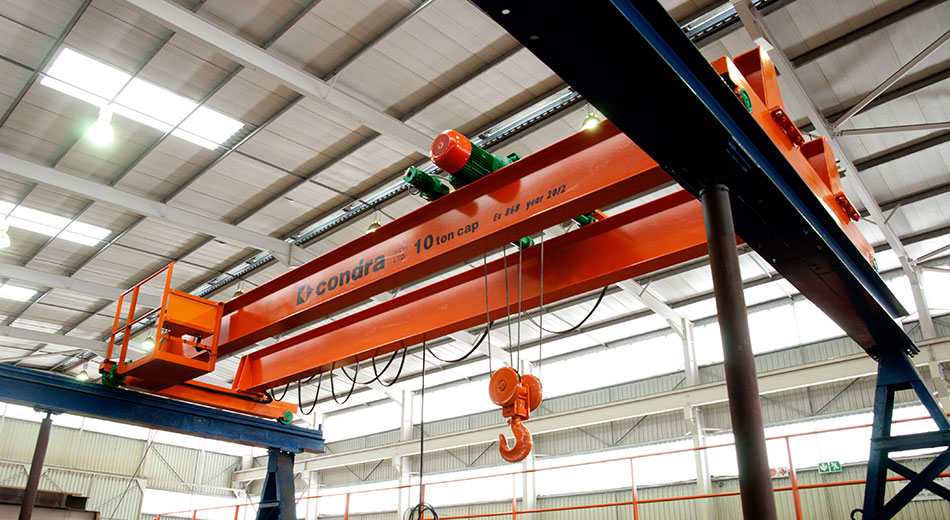
Typical Condra double-girder electric overhead travelling crane, similar in
arrangement to the seagoing crane, but with the motor drive delivered to steel wheels instead of rack-and-pinion.
Commenting on the order, Condra managing director Marc Kleiner said that the design of the crane had proved interesting not only because of the need to use rack-and-pinion drives, but also because of the very tight installation parameters within the vessel’s workshop, where ventilation pipes impose limits on the available space, and where careful design of the crane’s structure was needed to allow the hoist to be situated almost touching the workshop roof, thereby providing maximum lifting height.
“The resulting design is an underslung crane attached to the gantry beam rather than to the gantry columns. With the hoist sitting astride the underslung girders, we are able to give the customer the lifting height that he wants,” Kleiner said.
“It will be a compact but very effective arrangement.”
After delivery of the seagoing crane a few months from now, Condra technicians will carry out installation and commissioning in Durban at a much later date convenient to the customer, probably towards the end of the year when the vessel returns to harbour.